Active Flow Control for Wall-Normal Columnar Vortex
- US Patent Pending
Flow control is often employed to diminish the appearance of vortices or alter the characteristics of vortices in a liquid. For example, in a sump pump, the emergence of submerged vortices may degrade pump performance. If the submerged vortices are sufficiently strong, these vortices can include strong low pressure cores, which can entrain air/vapor along their vortex cores. If such hollow-core vortices are engulfed by the pump, they can cause unbalanced loading and vibration, leading to undesirable noise and possible structural failure. Strong wall-normal vortices appear inside and outside of many fluid-based machines as well as in natural settings, including tornadoes and hurricanes.
There have been numerous attempts to introduce passive vortex control techniques to prevent the generation of the aforementioned vortices or alter their pressure distributions. Yet passive control techniques do not offer the ability to adaptively adjust the control efforts to unsteady flow conditions (beyond design conditions). Moreover, some passive control devices are difficult to manufacture. Thus, these past efforts have shortcomings in offering reliable techniques to modify the pressure distribution of these vortices. Designing a more efficient and flexible vortex control strategy remains a challenge.
This invention is directed to spreading the core region of a coherent wall-normal vortex and alleviating the low-pressure in the core in a flow field. Such vortices are ubiquitous in nature and engineering systems, ranging from hydrodynamic/aerospace applications to nature, such as hurricanes and subsurface vortices. Many passive control techniques exist for wall-normal vortices, but none include active flow control methods that can be applied in an adaptive manner. In order to solve this problem, this technology introduces forcing input (e.g., fluid jet and suction) near the core region of the vortex to destabilize the local
flow and spread the core region. This in turn lowers the local angular velocity and increase the core pressure of the vortex. The increase of the pressure has engineering benefits because low pressure at the core can create detrimental engineering effects for vortices in air and liquids. In some instances, the forced input follows a sinusoidal form in time and in a co-rotating/counter-rotating direction for effective breakup of the vortex.
The invention provides a more adaptive technique than passive controls for alleviating the low-pressure effect of the vortex core using active flow control techniques. That is, the method of control provides a vortex control technique and device for vortices in different flow conditions. In order to achieve this, two different types of control strategies are disclosed based on co-rotating and counter-rotating mass injection and suction from the wall surface on which the vortex resides. The control strategy is employed on the wall where the vortex core is pinned and the mass injection/suction device is placed underneath the surface. The control input is adjusted with its frequency, amplitude, and direction of mass injection/suction.
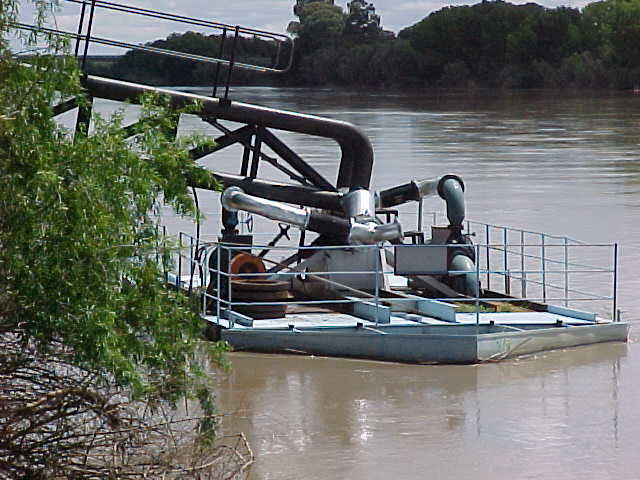
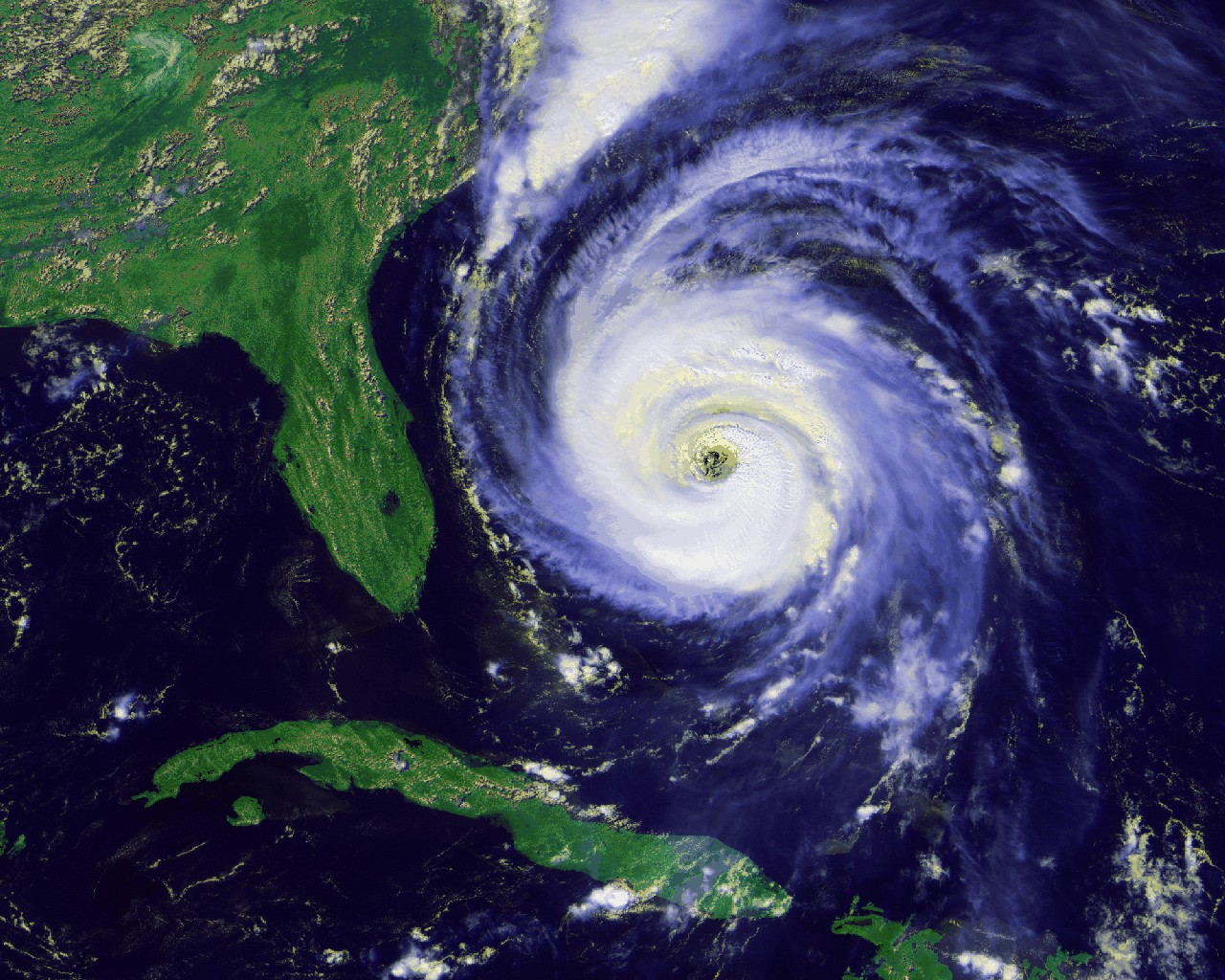